Home / News / Industry News / How do powder coating ovens and cures achieve proper adhesion and film formation?
Powder coating ovens and curing processes are essential in achieving proper adhesion and film formation in powder-coated metal. Here's how they contribute to the overall process:
1. Oven Design and Temperature Uniformity: Powder coating ovens are designed to provide uniform heat distribution throughout the curing chamber. This ensures that the entire surface of the coated metal reaches the desired curing temperature consistently, promoting even adhesion and film formation. Proper airflow within the oven helps maintain temperature uniformity.
2. Preheating: In some cases, a preheating stage may be employed before the curing process. Preheating warms the metal substrate, allowing it to reach a similar temperature as the powder coating. This minimizes the temperature differential between the substrate and the coating, reducing the potential for thermal shock and improving adhesion.
3. Curing Time and Temperature Profile: The curing time and temperature profile are critical factors in achieving proper adhesion and film formation. Powder coating manufacturers provide specific guidelines for the recommended curing conditions based on the powder coating chemistry. Following the manufacturer's instructions ensures that the curing process is optimized for the specific powder coating formulation.
4. Film Thickness Control: The thickness of the powder coating film plays a role in adhesion and film formation. Excessive film thickness can lead to inadequate curing, while a thin film may not achieve the desired durability. Proper control and measurement of the powder coating film thickness ensure optimal adhesion and film formation during the curing process.
5. Curing Methods: Different curing methods can be employed depending on the powder coating formulation and the equipment available. Convection ovens, infrared (IR) curing, and hybrid systems that combine convection and IR are commonly used. Each method offers advantages in terms of energy efficiency, cure speed, and control over temperature and heat transfer.
6. Curing Validation and Testing: To ensure the desired adhesion and film formation, quality control procedures may include testing the cured powder coating. Tests such as adhesion testing, hardness testing, and impact resistance testing can be performed to validate the quality and performance of the cured coating.
7. Cooling and Handling: After the curing process, the coated metal is allowed to cool down gradually to avoid rapid temperature changes that could affect adhesion and film integrity. Proper handling and cooling procedures are followed to prevent damage to the freshly cured powder coating.
8. Post-Curing Evaluation: Post-curing evaluations may be conducted to assess the adhesion, film quality, and overall performance of the powder coating. These evaluations ensure that the cured coating meets the required specifications for adhesion, appearance, durability, and resistance to environmental factors.
Powder Coated Metal Processing Manufacturers by carefully controlling the oven parameters, following recommended curing profiles, and conducting thorough quality control checks, powder coating ovens and curing processes ensure proper adhesion and film formation. These processes play a vital role in achieving durable, aesthetically pleasing, and long-lasting powder-coated metal products.
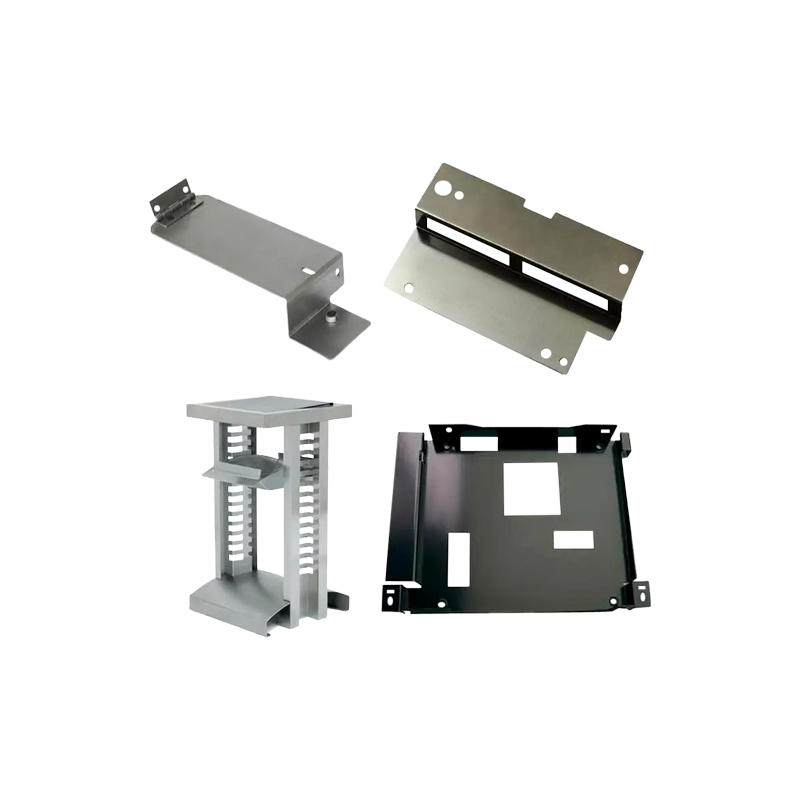
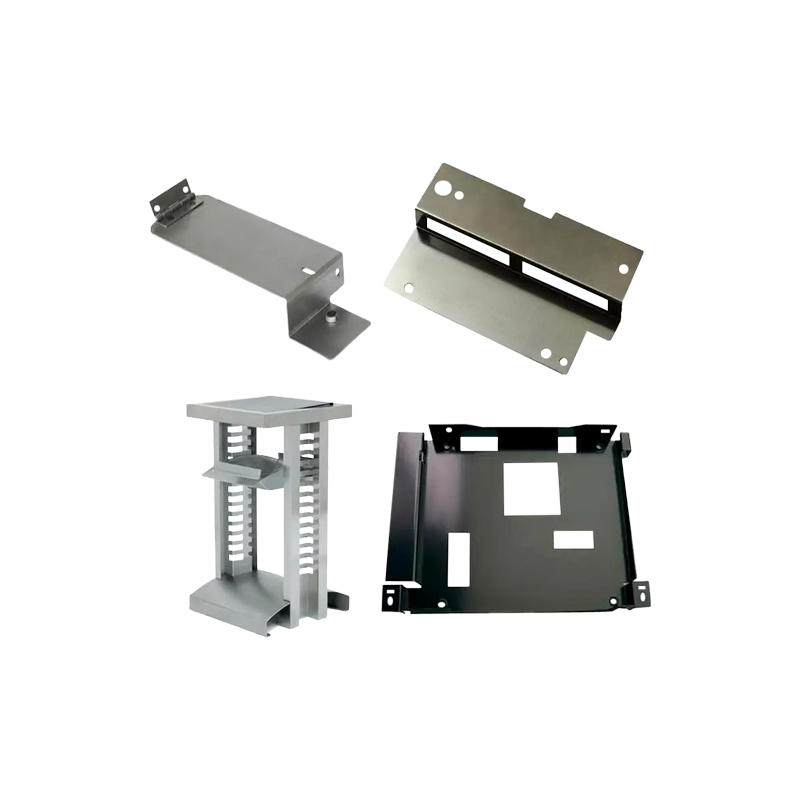
OEM Sheet Metal Processing Bending Punching Manufacturing Process Laser Cutting Stamping Fabrication
SUPPLY ABILITY
Supply Ability: 20000 Piece/Pieces per month
PACKAGING & DELIVERY
Packaging Details: Metal clamp packing shrink film + wooden box
LEAD TIME