Home / News / Industry News / What are the key tool and die design considerations in metal stamping?
Tool and die design is a crucial aspect of metal stamping, as it directly impacts the quality and efficiency of the manufacturing process. Here are some key considerations in tool and die design for metal stamping:
Part Geometry: The tool and Metal Stamping Manufacturer should accommodate the desired part geometry. This includes considerations such as the shape, size, thickness, and complexity of the part. The die components, punches, and cavities should be designed to accurately form the desired shape without distortion or defects.
Material Selection: The selection of materials for the tooling components is critical. They should have sufficient strength, wear resistance, and durability to withstand the forces and stresses encountered during the stamping process. Common tooling materials include hardened steel, carbide, and tool steels.
Die Clearance: Proper die clearance is essential to ensure smooth material flow and prevent issues like cracking, wrinkling, or tearing of the metal. The die clearance should be calculated based on the material properties, thickness, and desired part dimensions. It is crucial to strike the right balance between too tight or too loose clearances to achieve optimal results.
Strip Layout and Feeding: The design should consider the strip layout and feeding mechanism for efficient material utilization. Proper strip layout minimizes scrap and maximizes the number of parts produced per strip. The feeding mechanism should be designed to ensure smooth and accurate feeding of the strip into the stamping press.
Tooling Maintenance and Accessibility: Tool and die design should facilitate easy maintenance and accessibility for repairs, adjustments, and replacements. Proper clearances, access points, and removable components should be incorporated to streamline tooling maintenance and minimize downtime.
Tooling Life and Durability: The tool and die design should be robust and durable to withstand the repetitive nature of metal stamping. Factors such as material selection, heat treatment, surface coatings, and design features to prevent wear and fatigue should be considered to maximize tooling life and reduce the need for frequent replacements.
Lubrication and Cooling: Adequate provisions for lubrication and cooling should be considered in the tool and die design. Proper lubrication reduces friction and wear between the tooling components and the metal, while cooling helps dissipate heat generated during the stamping process, preventing excessive tool wear and thermal distortion.
Tolerance and Accuracy: The tool and die design should account for the desired tolerances and accuracy of the stamped parts. Careful consideration should be given to factors like dimensional control, spring-back, material elasticity, and any secondary operations required to achieve the desired part specifications.
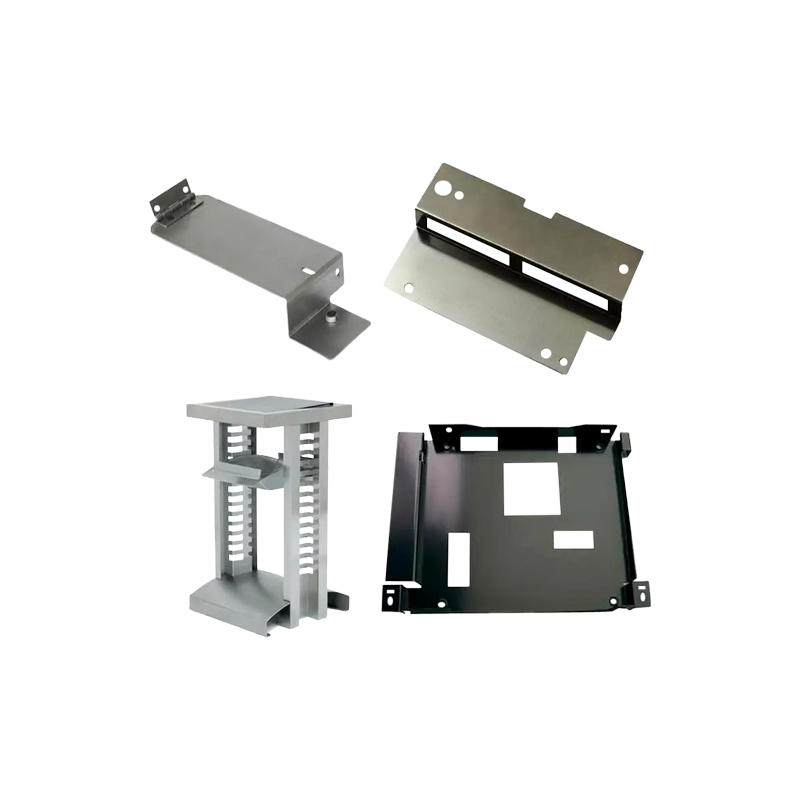
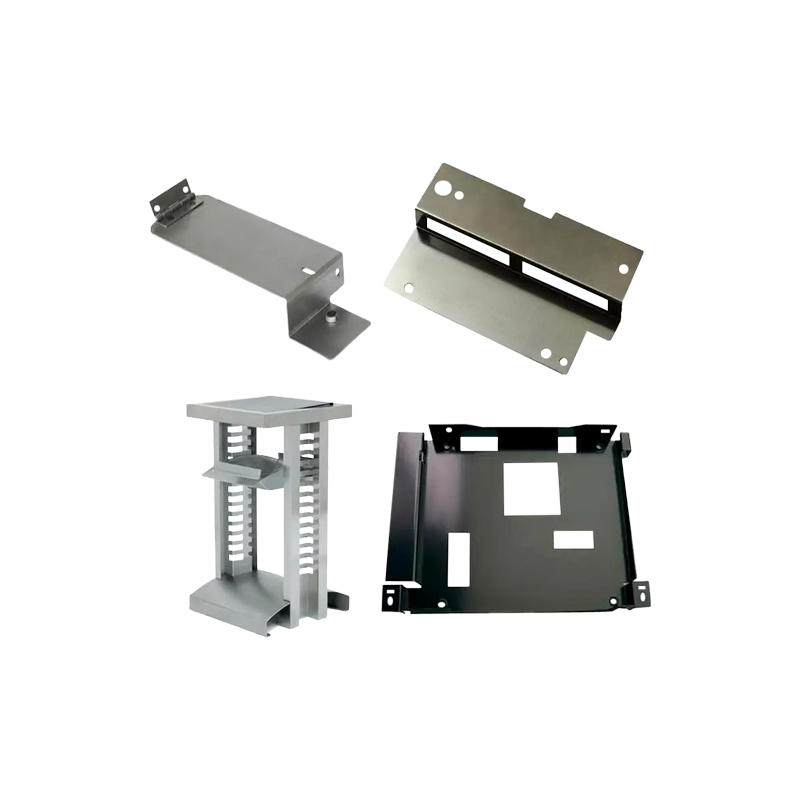