Home / News / Industry News / What considerations are crucial when selecting surface finishes for sheet metal parts to meet both functional and aesthetic requirements?
In the intricate world of sheet metal processing, the choice of surface finish plays a pivotal role in determining the functionality, durability, and aesthetic appeal of the final product. Whether destined for industrial machinery, consumer electronics, or architectural applications, sheet metal parts demand careful consideration when it comes to selecting the right surface finish. Striking a delicate balance between functionality and aesthetics requires an understanding of various factors that influence the decision-making process.
Functional Requirements: When delving into the functional aspects of surface finishes, the selection process becomes a nuanced examination of the specific environmental challenges a sheet metal part will encounter. Beyond merely considering corrosion resistance, it involves a meticulous evaluation of factors such as exposure to chemicals, potential wear and tear, and the overall lifespan of the part. For instance, sheet metal components operating in aggressive industrial settings, where exposure to corrosive substances is high, demand a surface finish with superior corrosion resistance. Understanding the intricacies of the operational environment ensures the chosen finish provides optimal protection and longevity.
Aesthetic Requirements: Aesthetic considerations extend far beyond the superficial desire for an attractive appearance. The intricate design elements, color palette, and texture of a sheet metal part become crucial components of the decision-making process. In industries where consumer appeal is paramount, such as consumer electronics or architectural design, the choice of surface finish becomes a strategic element of brand identity. The careful selection of colors and textures contributes not only to the visual appeal of the product but also to its market positioning and overall branding strategy.
Cost Considerations: The delicate interplay between aesthetics and cost-effectiveness involves a thorough analysis of budget constraints and long-term maintenance considerations. This encompasses an evaluation of the initial cost of applying a particular surface finish, as well as the potential costs associated with maintenance and reapplication over the product's lifecycle. Decision-makers must navigate the trade-offs between the visual impact of the finish and the financial implications, ensuring that the chosen finish aligns with both the project's budgetary constraints and the desired level of quality.
Durability and Lifespan: Durability considerations delve into the nuanced realm of scratch resistance, wear resistance, and the impact of environmental factors on the surface finish. A comprehensive evaluation of the expected lifespan of the finish is essential, considering factors such as the likelihood of scratches in the intended usage scenario and the impact of UV radiation on color stability. This multifaceted approach ensures that the chosen finish not only enhances the part's durability but also aligns with the intended aesthetic vision, providing a balance between longevity and visual appeal.
Application-Specific Considerations: Certain applications necessitate unique properties from sheet metal parts, requiring a customized approach to surface finish selection. For instance, applications demanding optimal electrical conductivity or specific thermal properties require finishes that either maintain or enhance these attributes. This tailored approach ensures that the sheet metal component not only meets functional and aesthetic criteria but also excels within the specific demands of its intended application.
Ease of Application: The practicality of applying a chosen surface finish within the sheet metal fabrication process is a pivotal consideration influencing manufacturing efficiency. This involves an intricate evaluation of the compatibility between the selected finish and fabrication methods, application techniques, and drying or curing processes. Choosing finishes that seamlessly integrate into the fabrication process streamlines operations, reduces production complexities, and enhances overall efficiency.
Oem Sheet Metal Processing Bending Punching Manufacturing Process Laser Cutting Stamping Fabrication
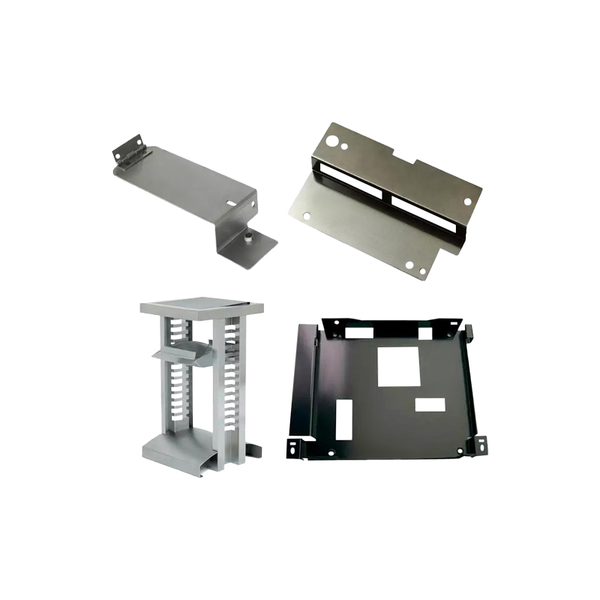
Oem Sheet Metal Processing Bending Punching Manufacturing Process Laser Cutting Stamping Fabrication
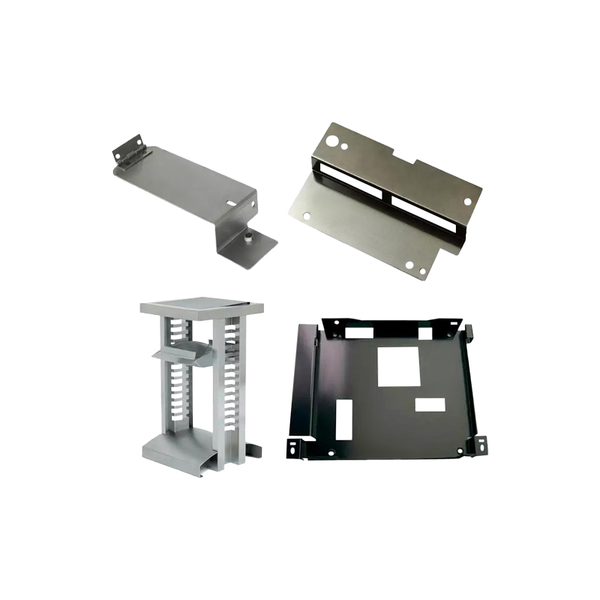