Home / News / Industry News / What considerations are there when choosing between batch and conveyorized powder coating systems for metal parts?
When choosing between batch and conveyorized powder coating systems for metal parts, several important considerations come into play. The decision should be based on the specific needs and constraints of your operation. Here are key factors to consider:
1.Production Volume:
Batch: Ideal for low to medium production volumes where frequent equipment setup changes are acceptable.
Conveyorized: Suited for high-volume production, ensuring continuous processing and optimized output for larger quantities of parts.
2.Throughput Efficiency:
Batch: Typically involves manual part loading, coating, and unloading, resulting in longer processing times and reduced throughput.
Conveyorized: Offers continuous and automated processing, minimizing downtime between batches, and achieving higher overall efficiency and throughput.
3.Cost:
Batch: Lower initial capital investment, making it more accessible for smaller operations or those with limited budgets.
Conveyorized: Involves higher upfront costs due to the necessary conveyor equipment and automation components but can offer long-term cost savings for high-volume operations.
4.Space and Layout:
Batch: Requires less linear floor space, making it suitable for facilities with limited space or irregular layouts.
Conveyorized: Needs a linear layout to accommodate the conveyor line and associated equipment, necessitating a larger floor area.
5.Flexibility:
Batch: Offers greater flexibility for coating various part sizes and shapes without significant system modifications.
Conveyorized: May require customizations to handle different part types effectively, potentially reducing adaptability for non-standard parts.
6.Processing Time:
Batch: Typically involves longer cycle times due to manual handling and the need for reloading between batches.
Conveyorized: Offers shorter and more consistent processing times, crucial for high-volume production with tight schedules.
7.Quality Control:
Batch: Requires more manual intervention and inspection, which can introduce variability in coating quality.
Conveyorized: Provides better control over coating consistency, curing times, and quality due to automation and continuous processing.
8.Energy Efficiency:
Batch: May consume more energy as it involves heating and cooling cycles with intermittent operation.
Conveyorized: Tends to be more energy-efficient due to continuous operation, minimizing energy wastage during startup and shutdown phases.
9.Labor Requirements:
Batch: Requires additional labor for loading and unloading parts, which can be a factor in overall operating costs.
Conveyorized: Reduces labor requirements, especially for repetitive tasks, as automation handles part movement.
10.Part Handling and Accessibility:
Batch: Parts may need to be manually positioned for coating, leading to variations in coating thickness and coverage.
Conveyorized: Designed for efficient and consistent part handling, ensuring uniform coating and ease of access for touch-up or rework.
11.Maintenance:
Batch: Typically has fewer moving parts and simpler equipment, resulting in lower maintenance requirements.
Conveyorized: May involve more complex components and additional maintenance to ensure smooth operation over time.
12.Material Handling Equipment:
Conveyorized: May require supplementary material handling equipment, such as overhead cranes or robots, to facilitate part transfer and positioning within the system.
13.Product Variety:
Batch: Well-suited for operations with a wide range of part sizes, shapes, or materials due to its inherent flexibility.
Conveyorized: Requires more careful consideration and customization to accommodate variations in part characteristics effectively.
14.Environmental Considerations:
Conveyorized: Offers the advantage of incorporating advanced environmental controls to capture overspray and emissions, contributing to a cleaner and more compliant work environment.
15.ROI and Long-Term Planning:
Batch: Considered for operations with lower initial budgets or smaller production volumes.
Conveyorized: Often provides a more attractive long-term ROI for large-scale production facilities due to higher efficiency and consistent output.
Oem Sheet Metal Processing Bending Punching Manufacturing Process Laser Cutting Stamping Fabrication
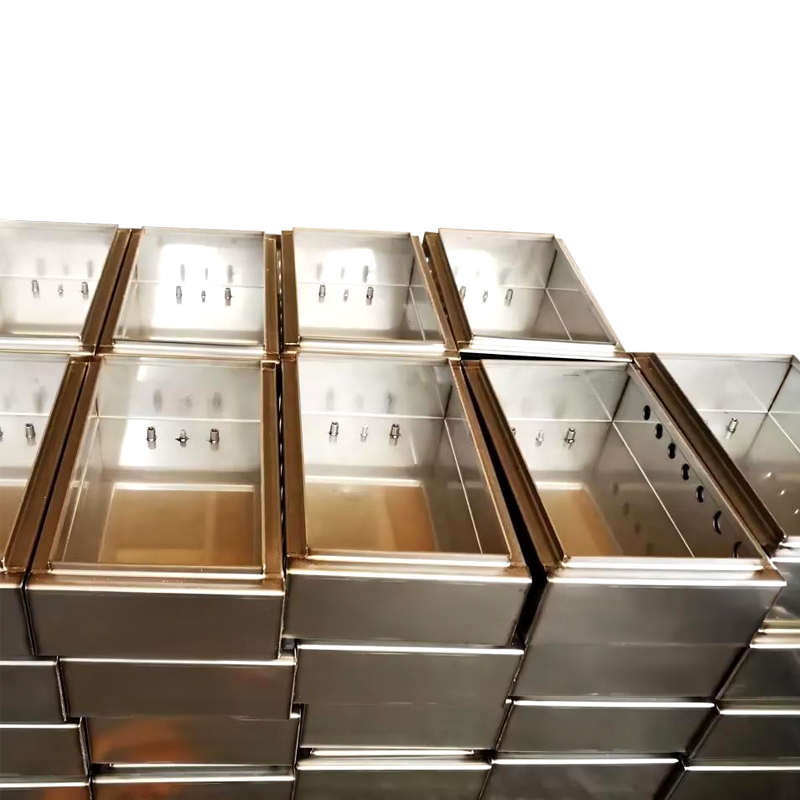
Model Number: Customized
Protection Level: IP65
Type: Sheet Metal Processing
External Size: Customized
Material: Stainless Steel, Aluminum, Carbon Steel, Galvanized Steel
Surface Finish: Powder Coating, Anodizing, Zinc Plating, Brushed or Polish