Home / News / Industry News / What is metal stamping, and how does it differ from other metal forming processes?
Metal stamping is a manufacturing process used to create metal parts from sheet metal. It involves the use of a stamping press and custom-made tool and die surfaces to shape, cut, or deform the metal into the desired form. The process can be used to produce a wide variety of parts, ranging from simple shapes to complex components used in various industries such as automotive, aerospace, electronics, and appliances.
Here's how metal stamping differs from other metal forming processes:
1.Precision and Complexity:
Metal stamping processes are engineered with precision in mind, capable of producing highly complex parts with tight tolerances. Engineers meticulously design the tool and die sets, ensuring that each stamped component meets the specified dimensional requirements. This precision is vital in industries where even minor deviations can compromise the functionality and safety of the final product.
2.Speed and Efficiency:
Metal stamping operations are inherently efficient and rapid, especially when automated. Stamping presses are designed to cycle quickly, allowing for the mass production of components in a short timeframe. The high-speed nature of the process significantly enhances productivity, making it indispensable for industries that demand large quantities of parts within tight production schedules.
3.Tooling:
Customized tool and die sets are the backbone of metal stamping. These tools are expertly crafted to match the exact specifications of the desired part. Tool and die engineers leverage advanced technologies and materials to create durable, high-precision tools. The investment in meticulously designed tooling ensures the consistent quality of stamped parts, making metal stamping a reliable choice for high-volume manufacturing.
4.Material Thickness:
Metal stamping is ideally suited for thin-gauge materials. Its proficiency lies in shaping sheets of metal into intricate forms. Thin materials, which might be impractical for processes such as forging due to their low formability, can be efficiently transformed through stamping. This makes the process valuable for applications where lightweight yet sturdy components are required.
5.Material Waste:
Metal stamping minimizes material wastage. By precisely cutting parts from flat sheets, the process generates minimal scrap. This eco-friendly approach not only reduces material costs but also aligns with sustainable manufacturing practices, making it an environmentally conscious choice for companies aiming to minimize their ecological footprint.
6.Versatility:
Metal stamping is versatile, accommodating a wide array of metals and alloys. Whether it's steel, aluminum, brass, or specialized alloys, stamping processes can be tailored to suit the material's unique properties. This adaptability ensures that manufacturers can select the most appropriate metal for the application, balancing factors such as strength, conductivity, and corrosion resistance.
7.Complex Geometries:
The flexibility of metal stamping enables the production of components with intricate geometries. Engineers can design stamping dies to incorporate complex features such as flanges, bends, and fine details. This ability to create multifaceted shapes is especially advantageous in industries like automotive and electronics, where components often have intricate designs to optimize performance and functionality.
8.Cost-Effectiveness:
While the initial investment in tooling can be significant, metal stamping offers remarkable cost efficiencies for large production volumes. The rapid production rates, minimal material wastage, and precise manufacturing lead to a low per-part cost. Over extended production runs, the initial tooling costs are amortized, making metal stamping an economically viable choice for businesses focused on long-term cost-effectiveness and high-quality output.
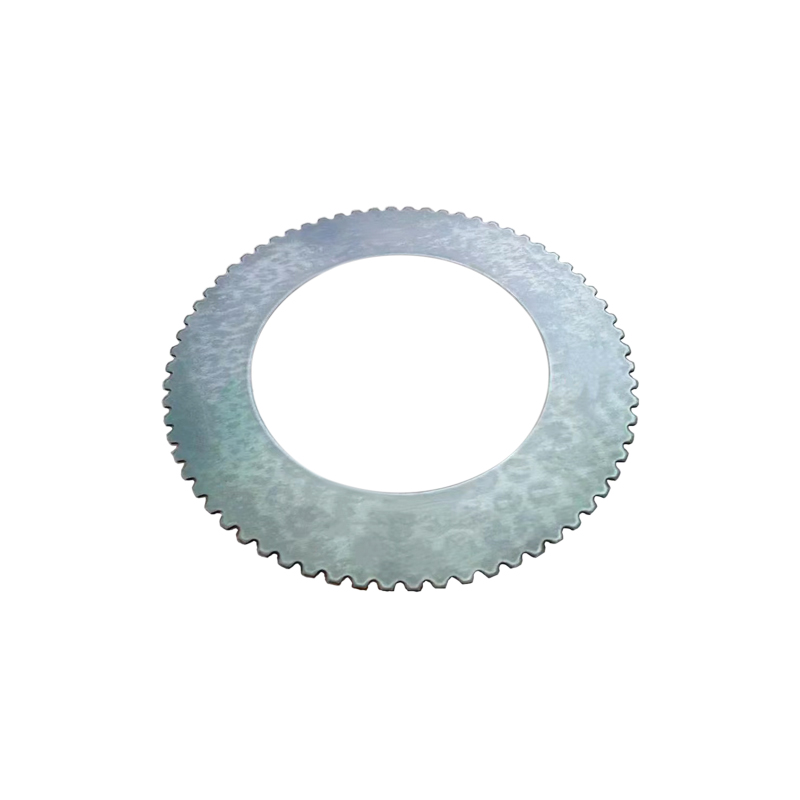
Model Number: Customized
Size: Customized
Material: Carbon Steel, Paper Base and Copper